Development of a new test bench by the Innovation Center
Date: - Categories: Innovation
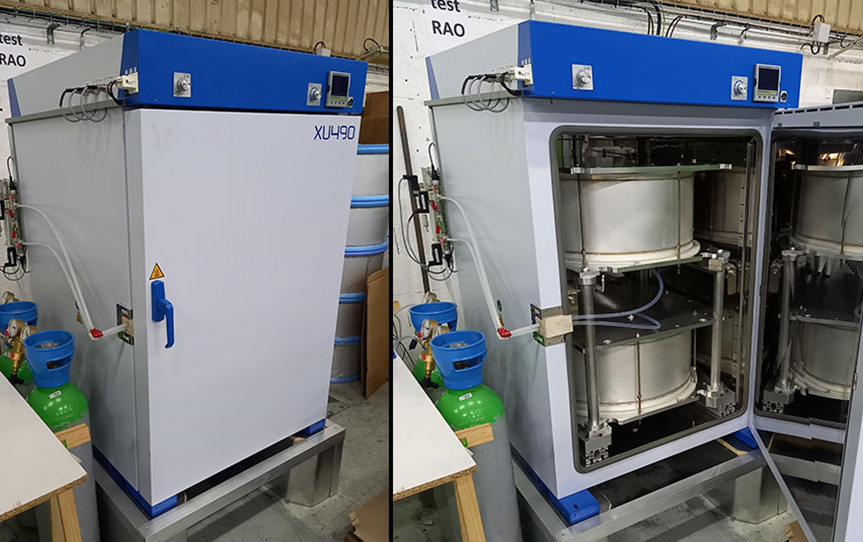
We manufacture on our industrial site of Laxou parts that are part of the air conditioning distribution system of the A350. These cylindrical parts, resulting from a manufacturing process including rolling and welding, must meet precise temperature and pressure resistance requirements.
The challenge
To design a compact leak test bench, allowing the control of the parts two by two, in a simple and ergonomic way, internally and directly on their place of manufacture.
The solution
In partnership with our client, the Group’s Innovation Center has designed all the necessary elements for the development of this solution:
- Choice of the oven to accommodate two parts, a structure and the mechanical handling systems.
- Electrical adaptation of the oven to allow autonomous control.
- Development of a mechanical system for placing and extracting the parts and accessories used for pressurization, while respecting minimum space constraints.
- Development of the automated pneumatic circuit, respecting the temperature cycle (pressurization, solenoid valve…).
- Development of a software interface (data recording and processing, generation of a report in the form of a PDF document containing the reference elements of the controlled part, the « Conform » or « Not Conform » information and the pressure resistance curve at different temperatures).
The benefits
By integrating this test bench into our manufacturing process, we provide our customer with several benefits: a reduction in the cost of the part, a shorter manufacturing lead time for the tested part, and greater flexibility for its supply flows.
It also has a positive influence on our carbon footprint with a reduction in transport and packaging!
You have a similar challenge? Please get in touch with us.